blow molding Introduction
Extrusion blow molding is the largest process user of high-density polyethylene (HDPE). “Plastic News” reported through September 2008 that United States production of HDPE was 12.8 billion pounds. The extrusion blow molding markets for HDPE that are growing at a greater pace than the bottle market, in general, are for large holding tanks, 55 gallon drums, and automotive fuel tanks. Approximately 40% of the HDPE produced goes into the blow molding market, making it the workhorse process of the HDPE industry.
Blow molding is the forming of a hollow object by inflating or blowing a thermoplastic molten tube called a “parison” in the shape of a mold cavity. The process consists of extruding or “dropping” a parison on which female mold halves are closed. The female mold halves contain the shape of the product to be produced. The bottom opening of the parison is pinched shut by the closing female mold halves. A pressurized gas, normally air, is introduced into the parison blowing the heated parison out against the cavity walls to form the product
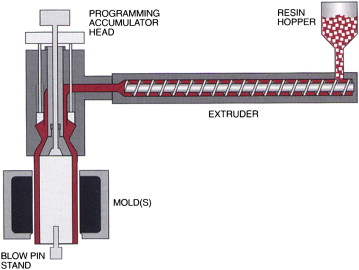
The formed part cools as depicted in Figure crystallizes, and is further cooled in the blow mold until it can be removed from the blow mold and retain the desired shape without warping.
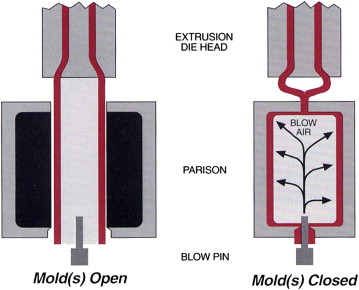
Latest News
Latest News
Contact Us
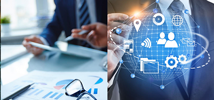
Name: Ms.Apple
Tel: +86 76986298860
Mobile: +8613528556448
E-mail: [email protected]
QQ: 332128783
WeChat: +8613528556448
Whatsapp: +8613528556448
Add: 121 Junfa 3rd Road, Dongkeng Town, Dongguan City, Guangdong Province, China